Automated parts washers are essential in pharmaceutical manufacturing for cleaning equipment parts with consistency and reduced variability compared to manual cleaning. This improves the ease of validation and ensures critical cleaning parameters (temperature, time, agent concentration, etc.) are consistently applied.
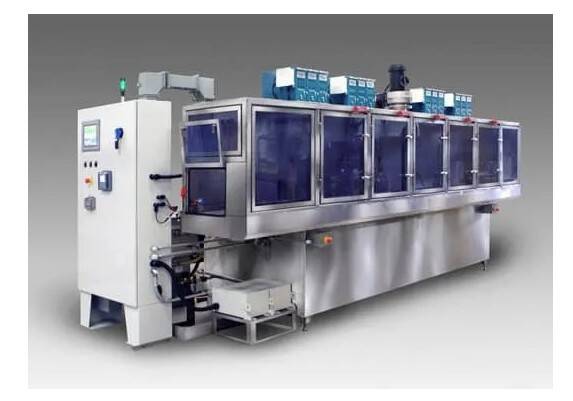
The goal of this article is to propose a standardized, science-based validation approach using the process validation lifecycle outlined by the US FDA. The lifecycle includes three stages:
Stage 1 – Process Design:
- Define Critical Quality Attributes (CQAs) for cleaned parts.
- Specify equipment requirements and design cleaning cycles.
- Identify and optimize Critical Process Parameters (CPPs) like time, temperature, detergent concentration, and spray configuration.
- Assessment of worst case product or soil
- Assessment of load configuration and define loads
- Assess and Define sampling strategy and sampling locations and rational
- Define cleaning agent / detergents to be used with rational
- Establish test acceptance criteria and analytical method
- Conduct lab trials with worst case soil and load to establish cleaning effectiveness.
- Final deliverable: a Cleaning SOP with clearly documented CPPs.
Stage 2 – Process Qualification (IQ/OQ/PQ):
- Confirm that the cleaning SOP is robust and reproducible.
- Develop and execute a cleaning validation protocol.
- Validate using actual parts, assessing cleaning via analytical methods (e.g., TOC, swabs, visual).
- Final report confirms the process is validated.
Stage 3 – Continued Process Verification:
- Monitor the cleaning process to maintain control.
- Perform preventive maintenance, periodic reviews, and risk-based evaluations.
- Assess change controls and CAPAs to identify the need for revalidation or optimization.
Cleaning Validation approach to its Lifecycle:
The main goal of Stage 1 is to fully understand the design and cleaning needs of the equipment. This upfront investment helps ensure success in Stage 2, the process qualification phase. During this stage, the automated parts washer is specified (via URS, FS, DS), qualified (FAT, SAT, IQ, OQ), and the cleaning cycle is developed for future validation (PQ).
Before the washer is delivered, a Factory Acceptance Test (FAT) should be conducted to confirm the machine works as intended. This can include coverage tests and full cleaning trials using soiled parts. A thorough FAT can reduce the work needed for final qualification once the washer arrives onsite.
When developing the cleaning cycle, lab trials should be performed using coupons (material samples) that simulate real-world conditions. These coupons can be soiled with a “master soil,” either a typical or worst-case residue. Trials help determine the best cleaning parameters—like detergent concentration, temperature, and mechanical action—before the washer is installed. This helps define CPPs early, saving time and resources later.
The key output from Stage 1 is a cleaning Standard Operating Procedure (SOP), where all process parameters are documented. These include:
- Spray device design and positioning
- Loading setup inside the washer
- Dirty hold times
- Water/solution temperature
- Cleaning agent concentration
- Rinse/wash cycle duration
- Clean hold times and storage conditions
Stage 2 confirms that the cleaning SOP works consistently and effectively. A cleaning validation protocol is created, which outlines the strategy, load setups, CPPs, sampling methods, and cleanliness criteria (e.g., drug residue, TOC, conductivity). After executing the Performance Qualification (PQ), a final report is generated to confirm the cleaning process is validated and to highlight any ongoing monitoring needs.
Stage 3, the continued process verification phase, ensures the cleaning process remains in control over time. This includes preventive maintenance, regular review of performance data, and monitoring for any changes. Equipment maintenance should follow manufacturer guidelines, and periodic reviews should cover process data, test results, investigations, and any system changes that could require revalidation. Risk analysis tools can help identify areas for improvement or revalidation.
Spending time in Stage 1 to deeply understand the washer and cleaning process is crucial. This knowledge helps in troubleshooting issues later. If problems arise, lab tests can recreate failures to support root cause analysis. This may lead to updates in risk assessments and reveal opportunities for optimization or tighter process controls.
Conclusion:
Adopting a lifecycle approach to cleaning validation enhances control, consistency, and continuous improvement in automated parts washer processes. Investing time in development ensures long-term process reliability and regulatory compliance.
Add comment
Comments